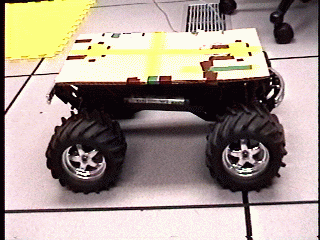 | The base RC-car mobile
platform, prepared for our first video shoot, in which we simply
mounted a camcorder on it and drove it manually. |
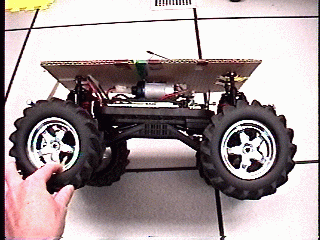 | The car runs at 25 MPH for
about 20 minutes on a standard set of two 7.2V battery packs. We will
equip the beobots with four packs and many additional Li-Ion camcorder
batteries to power the on-board quad-CPU Beowulf. Ruchi has found cool
battery packs and DC/DC converter chips which we are experimenting
with. |
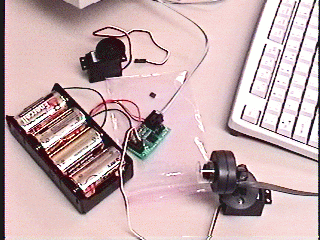 | Controlling the
servomechanisms (which allow the robot to turn, accelerate, brake and
switch between first and second gear) is working using a
serial-to-servo converter and some software which Jen developed. Jen
is now putting together a servo-based pan/tilt camera mount for the
beobots. |
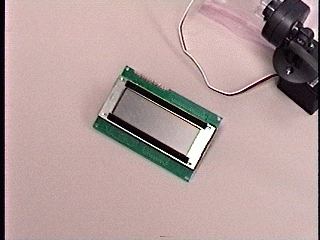 | Software to control the
diagnostic LCD screen from a standard PC serial port is almost ready,
from Jen and Paul. |
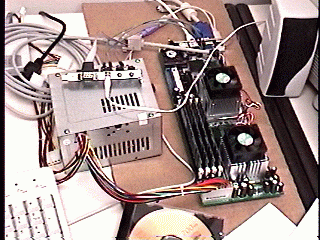 | The dual-CPU embedded
motherboards (Rocky-3742EVFG, purchased from www.histar.com.tw) are
working great. Eric installed Linux Mandrake 8.1 on a 256MB
CompactFlash disk, and it was a breeze. The Gigabit Ethernet chip
(which will link both boards in each beobot) was not automatically
recognized during installation, but a kernel module is available for
it, so it was trivial to configure. The default kernel did not include
support for 1GB of memory, so we are cooking up a custom kernel with
all the drivers required for the board. Video, sound, ieee1394,
serial, parallel, etc are all working great under Linux. |
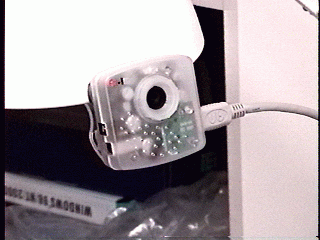 | We just wrote a high-level
driver for these cool firewire (IEEE-1394) cameras. Each Beobot will
have two such cameras, mounted on a pan/tilt head composed of two
servomechanisms. |
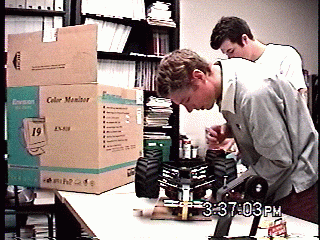 | Eric and Tony finish to
prepare the robot for its first trip outdoors (under human
control). Check it out here (8.5 MB
MPEG movie, 30 fps). In this movie sequence, the attention model has
its internal memory (inhibition of return) turned on, so, once it
looks at any given object, it will not come back to it for a few
seconds. In this respect, the attentional fixations shown in this
movie differ from ours, as we tend to continuously fixate one
interesting object when we find one that is relevant to our current
task. Note how the model does find most interesting objects in the
scene (hands, people, trees, pillars) though it only very briefly
attends to each one. The autonomous beobots will use a combination of
our attention model (to find possible obstacles and landmarks), a
navigation system based on a rapid computation of the gist of the
scene (where the road is, where the sky is, etc), and localized object
recognition linked to the attention model, so that we can identify
the targets being attended to. |
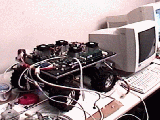 | Nathan completed soldering
together a prototype of our infernal power conversion system, which
delivers up to 34A @ 5V to the CPU boards from batteries. Looks like
we can power all four CPUs for slightly over an hour from 8 standard
R/C battery packs. Great! |
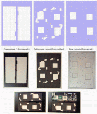 | Mounting
the CPU boards onto the car chassis was challenging because the CPU
boards have no mounting holes pre-drilled in them, and component
density is so high that there is absolutely no room to drill anywhere
on the boards. April found a great way of solving thie problem: the
CPU boards rest on a rubber mat in which appropriate cut-outs have
been laser-cut to accommodate for the various components soldered on
the back side of the CPU boards. The rubber mat rests on a solid piece
of laser-cut clear acrylic, the base board. Finally, a piece of thin
laser-cut acrylic fits tightly around the CPU boards so that they
cannot shift. The CPU boards are then maintained in place by many
screws just adjacent to the CPU boards, so that the screw heads hold
the boards without requiring any drilling into the boards. Click here for a larger image. |
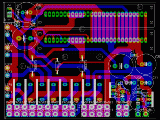 | The final version of our
infernal power conversion system is ready for fabrication. The
schematic diagram and printed circuit board layout were done using the
freeware version of Eagle PCB software from Cadsoft. The circuit just
fits within the 3x4in maximum board size available in the freeware
vesion of Eagle PCB. Thank you Cadsoft! |
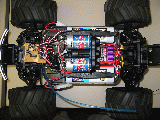 | Daesu completed a simple
circuit (shown in front of the two motors) that allows us to switch
between PC-controlled and radio-controlled by flipping a switch on the
radio controller. This will allow us to easily take over the control
of the robot in case of bug in our vision algorithms. |
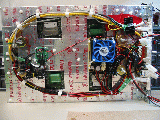 | The main platform, shown
here from below, is ready to go. On the left, the mini-SSC interfaces
the PCs to the car's servomechanism. On the right, the fan-cooled
power conversion module delivers power to the CPUs from camcorder
battery packs. |
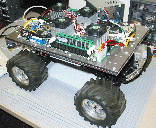 | The first
prototype is basically ready and working; the last few components
missing on this picture are the batteries, the protective shell, and
the pan/tilt camera mounts. |
 | Hook it up,
install Linux Mandrake 8.2 on the flash drives, and off you go!
|
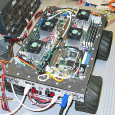 | This laser-cut
control panel at the back of the robot was a real pain to assemble,
because we had to cut and solder a zillion custom cables. But it is
really useful to connect the beobot to a monitor, keyboard, mouse,
GPS, speakers and microphone, various USB devices, etc. |